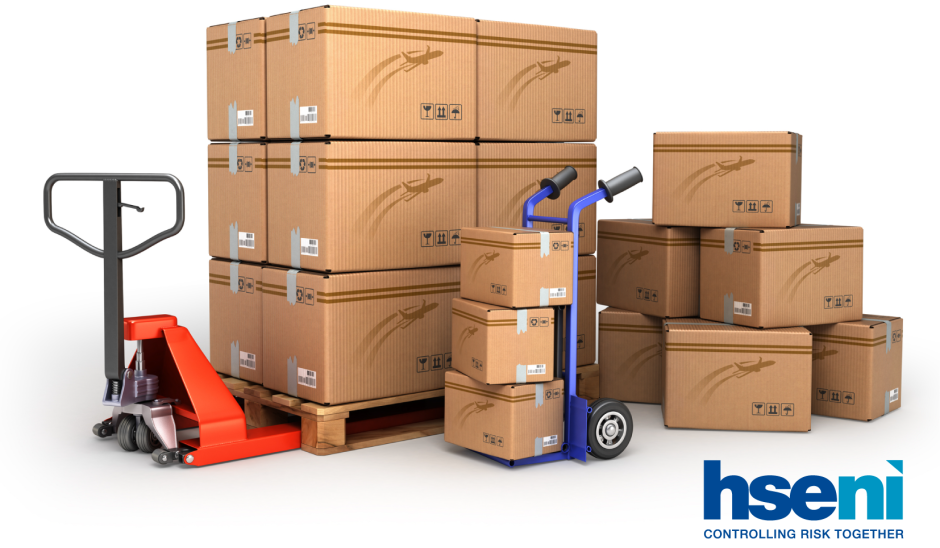
What is manual handling?
In general terms, when a worker lifts, carries, pushes, pulls, moves, or supports a load using their hands or bodily force they are involved in manual handling at work.
Manual handling activities in the workplace can vary from low-risk activities such as carrying light weight items, for example bundles of paper, to higher risk activities such as moving heavy boxes by hand, to very high-risk activities including repetitive lifting of medium weight items continually during a shift or pushing/pulling of very heavy items within the work area.
Manual handling risks are prevalent across all industries and can be found in most workplaces including construction sites, farms, factories, hospitals, nursing homes, schools, workshops, etc. Repetitive tasks are typically found in assembly, production and packaging, as well as work involving regular use of hand tools.
Factors that can affect the level of risk, whilst not exhaustive, include:
- load weight
- task duration
- frequency of the task
- distance to be travelled
- bodily movements - i.e. bending, twisting, and/or stretching
Heavy items present the most obvious risk, however frequent, poorly handled loads also present a risk.
Heavy manual labour, repetitive handling, awkward postures and previous or existing injuries or conditions are all risk factors for sustaining or exacerbating manual handling injuries or musculoskeletal disorders (MSDs) due to the physical activities which individuals carry out. Workers with previous injuries are at an increased risk.
Manual handling injuries, such as pain in the back, lower and/or upper limbs, are part of a wider group of musculoskeletal disorders (MSDs).
Work-related MSDs and back injuries from manual handling operations are a major cause of occupational ill health in all industries across Northern Ireland, however:
- they can often be prevented
- preventative measures can be cost-effective
- where injuries occur, early reporting of symptoms, proper treatment and suitable rehabilitation is essential
How do I manage workplace manual handling operations?
The best approach to injury prevention is to eliminate the risk by avoiding the manual handling operation or by automating it.
Handling aids can remove or reduce risk, keeping workers healthy and at work, however poorly considered handling aids may bring about other risks such as those caused by unsuitable equipment or untrained staff.
Employers responsibility
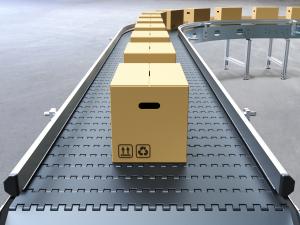
Employers have a legal duty under the Manual Handling Operations Regulations (Northern Ireland) 1992 (MHOR) to manage the risks to employees involved in manual handling operations at work.
The Regulations establish a clear hierarchy of control measures. Risk assessments associated with manual handling operations must show that these control measures have been considered
To comply with legislative requirements, employers must:
- avoid hazardous manual handling operations, so far as is reasonably practicable - for example, by redesigning the task to avoid moving the load or by automating or mechanising the process
- make a suitable and sufficient assessment of the risk of injury from any hazardous manual handling operations that cannot be avoided
- reduce the risk of injury from those operations, so far as is reasonably practicable - for example, provide mechanical assistance where possible such as a sack trolley or hoist (where this is not reasonably practicable then changes to the task, the load and the working environment should be explored)
Where manual handling cannot be avoided, it is important to work in a systematic manner and to structure the approach to assess and reduce the manual handling work activity to prevent work-related injury and for the effective management of manual handling operations.
It is important to consider manual handling operations in the workplace taking into account all workers involved. People come in varying shapes and sizes, and those who are of taller or shorter height may struggle with fixed position workstations.
Employees responsibility
Employees are also legally obliged to ensure that they adhere to any guidance, instruction or training provided by their employers.
Employees will often know what the risks are within the workplace and are well placed to offer practical solutions to controlling those risks. Therefore, employee consultation and engagement will prove beneficial with the management of workplace manual handling operations.
Assessment of workplace manual handling risks
Undertaking a risk assessment may seem complicated, however is simply a structured way of analysing risks and should enable the assessor, in consultation with relevant employees, to develop practical solutions.
Where a risk of injury is identified for manual handling operations and avoidance of the risk is not reasonably practicable, a more specific risk assessment is required by law.
There are key factors which must be considered as part of any manual handling assessment for which the acronym TILEO is often used.
The key factors include:
- Task
- Individual capability
- Load
- Environment
- Other factors
Assessment of manual handling risks using an ergonomic approach will be subjective to the assessor.
Involve employees and safety representatives during assessment and when considering possible lifting aid solutions, so that you can be sure what you propose will work in practice and won’t introduce any new hazards.
The Health and Safety Executive (HSE) have produced a guidance document, L23 on the Manual Handling Operations Regulations, which introduces the concept of risk filters or numerical guidelines.
These guideline figures set out an approximate boundary within which the load is unlikely to create a risk of injury. It should be noted that the guideline figures are not “weight limits” or “safe limits”.
In general terms, if the load is within the numerical guidelines then it may not be necessary to do any other form of risk assessment.
Risk filters or numerical guidelines exist for the following manual handling operations:
- lifting and lowering
- pushing and pulling for up to 20m
- carrying for up to 10m
- handling while seated
The numerical values for lifting and lowering are reduced if handling is done with arms extended, or at high or low levels. The guidelines assume the load is easy to grasp with both hands, the operation takes place in reasonable working conditions and the handler is in a stable body position. An assumption is also made that the employee is in reasonable health.
What tools are available to assist employers?
The HSE has produced a series of tools designed to guide users through logical processes to identify high-risk manual handling operations.
The Manual handling assessment charts (MAC), Assessment of repetitive tasks of the upper limbs (ART) and Risk assessment of pushing and pulling (RAPP) tools have been designed to simplify the process of completing each assessment and reduce subjectivity of the assessment.
The MAC tool will help to identify high-risk manual handling activities within the workplace.
Each of these HSE’s risk assessment tools adopt a logical step-by-step approach and will save an assessor considerable time in populating the results manually. They incorporate numerical and colour-coding score systems to highlight high risk manual handling tasks.
Employers can use these tools to easily assess the risks posed by physical, strenuous activities.
The assessor can then understand, interpret, categorise, and communicate the level of risk of the various known risk factors associated with manual handling activities.
Depending on the task, you may find it helpful to use more than one tool, for example you may need to pick up a box of items (lifting), carry it to a workstation (carrying), then distribute the contents to other locations such as pigeon-holes or a filing cabinet (repetitive movements).
Common Questions and Answers
For a list of common questions and answers regarding manual handling, please see the following link:
Resources
- Back pain
- Reducing the manual handling of roof panels - Information Sheet - (hsa.ie)
- Guidance on the Prevention and Management of Musculoskeletal Disorders (MSDs) in the Workplace
- Handling with care - A guide for the healthcare sector
- Reducing manual handling of plasterboard - Best practice guidance
- Assessment of repetitive tasks of the upper limbs (ART Tool) (INDG438) - (hse.gov.uk)
- Getting help with manual handling risks in your business - (hse.gov.uk)
- Full manual handling risk assessment: Examples of assessment checklists - (hse.gov.uk)
- Making the best use of lifting and handling aids (INDG398) - (hse.gov.uk)
- Manual Handling Operations Regulations 1992 - Guidance on the Regulations (L23) - (hse.gov.uk)
- Manual handling at work - A brief guide (INDG143) - (hse.gov.uk)
- Manual handling assessment charts (MAC tool) (INDG383) - (hse.gov.uk)
- Manual handling - What you need to know as a busy builder (CIS61) - (hse.gov.uk)
- Preventing injury during plasterboard handling (CIS76) - (hse.gov.uk)
- Preventing injury from handling heavy blocks (CIS77) - (hse.gov.uk)
- Reducing plasterboard manual handling (COH05) - (hse.gov.uk)
- Risk assessment of pushing and pulling (RAPP) tool (INDG478) - (hse.gov.uk)
- Lower limb disorders (LLDs)
- Upper limb disorders (ULDs)
Key Legislation
- Health and Safety at Work (Northern Ireland) Order 1978 - (legislation.gov.uk)
- Health and Safety at Work (Amendment) (Northern Ireland) Order 1998 - (legislation.gov.uk)
- Management of Health and Safety at Work Regulations (Northern Ireland) 2000 - (legislation.gov.uk)
- The Management of Health and Safety at Work (Amendment) Regulations (Northern Ireland) 2006 - (legislation.gov.uk)
- Manual Handling Operations Regulations (Northern Ireland) 1992 - (legislation.gov.uk)
Please note that these links are to the original legislation, visitors should verify for themselves whether legislation is in force or whether it has been amended or repealed by subsequent legislation.