Introduction
This information sheet is being provided to Industry, to enable duty holders to assess the suitability of their current guarding arrangements at return idlers, and where necessary, carry out improvements to remove the risk of trapping and crushing hazards. The Provision and Use of Work Equipment Regulations (NI) 1999, sets out the legal requirement for employers to prevent access to dangerous parts of machinery. This can be achieved by the fitting of adequate guarding arrangements.
Return idlers are an important part of any conveyor system and are used to support the weight of the return belt. It is important that accessible nip points at conveyor return idlers on both fixed and mobile equipment are adequately guarded to prevent the risk of a serious injury or fatality.
In-running nip points on a typical conveyor system are shown in the following image:
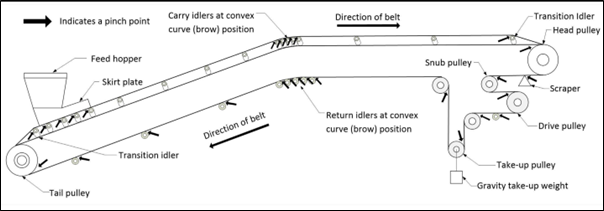
The nip point is the dangerous pinch point which may occur at the line of contact between the rotating return idler and the moving conveyor belt on the in-running side of the idler. Where a nip point on a return idler of a conveyor is accessible (within 2.7 metres reach - including those return idlers accessible from conveyor catwalks) it must be guarded.
There are different types of return idler guards available to prevent access to in-running nip points and remove the risk of trapping and crushing hazards. Safeguards may be in the form of fixed close guards, distance guards or nip guards.
Fixed close guards
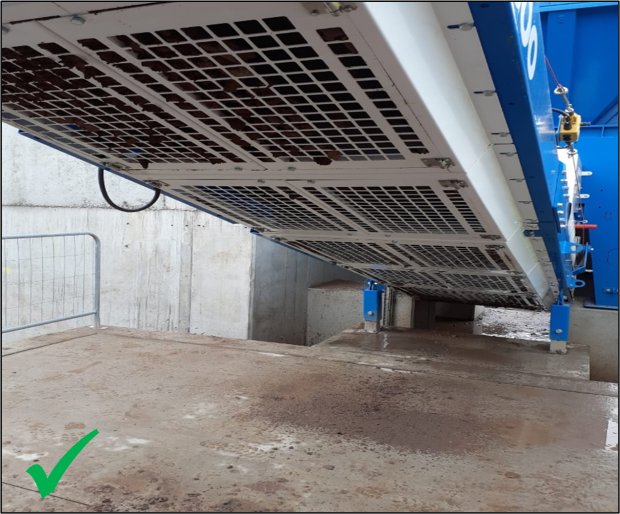
A suitable open mesh guard can be fitted to either side of the return idler.
The guard must ensure that it is not possible for persons to reach into the in-running nip point of the return idler.
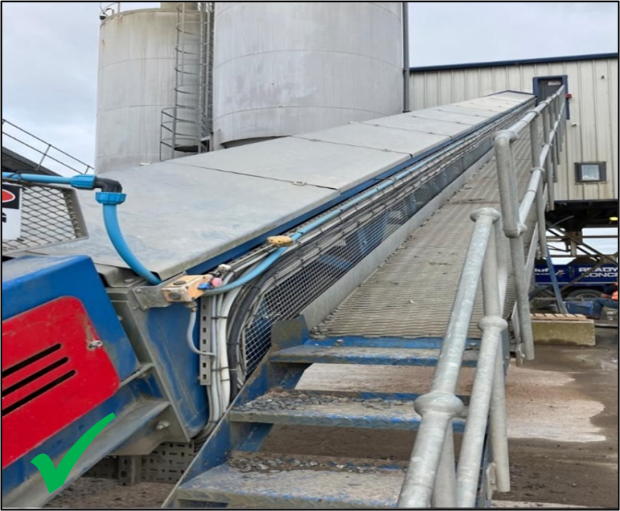
Mesh apertures should be sized to prevent the accumulation of material inside the guard yet must also prevent finger or hand contact with the nip points within.
Make guards safer by design to enable maintenance such as greasing, cleaning and tracking to be completed without having to remove the guard.
Where periodic removal of the guard is required an effective isolation and lockout procedure must be in place.
Distance guards
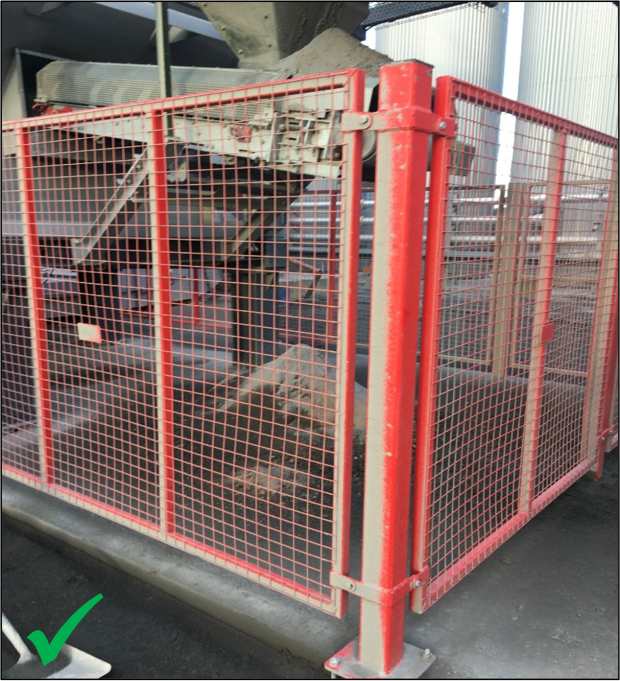
Where panel type perimeter guards are fitted (for example at horizontal feed conveyors), guards should surround the conveyor and be securely fixed to the structure or foundations.
The minimum height of the guard should be two metres.
Access gates should be secured using a suitable captive key system or electrically interlocked system.
Remote greasing points should be provided to enable lubrication to be carried out without entering the guarded area.
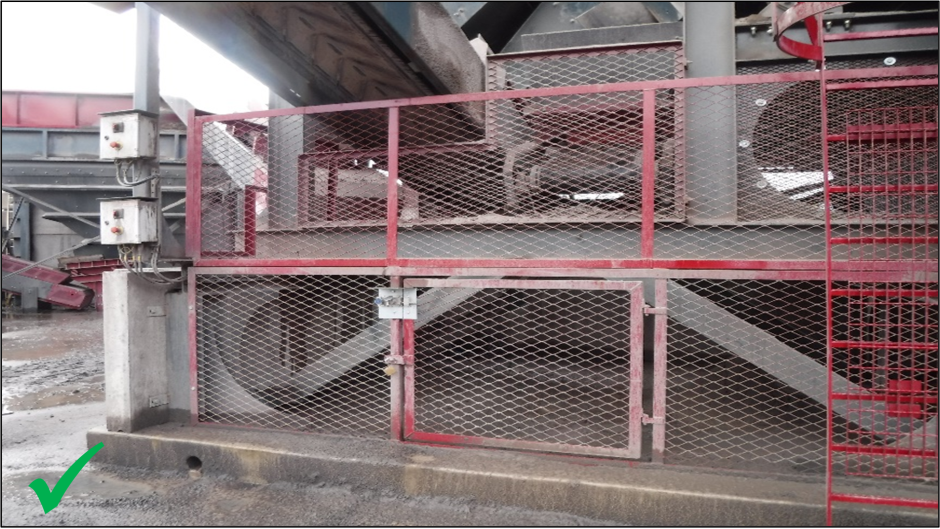
Nip guards - Good practice
A nip guard is a fixed guard fitted at the nip point to directly safeguard that point.
Plate type nip guards are commonly fitted at conveyor return idlers.
These plate type nip guards must be designed and fitted correctly to prevent access to the in-running nip points and therefore remove the risk of trapping and crushing hazards.
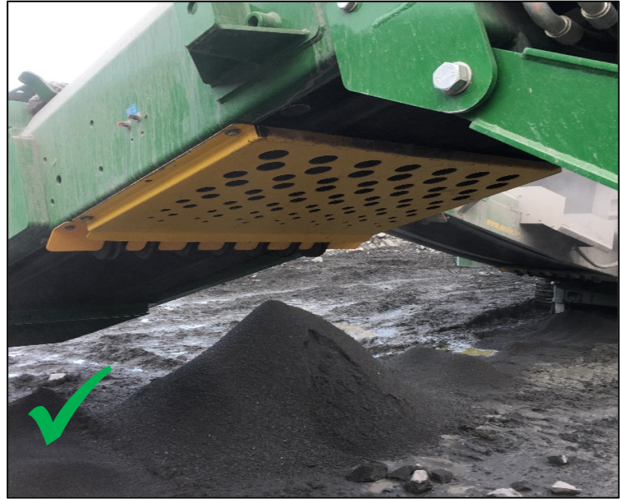
If a plate type nip guard is fitted but it is still possible to reach into the in-running nip point of the return idler, the guard is not suitable and an alternative guard will be required.
The plate type nip guard shown has been fitted with a plate on the upper side of the belt which ensures that the guard follows the belt line and that the nip point is not accessible.
Nip guards - Bad practice
The following plate type nip guards did not prevent access to the in-running nip point. It was possible for persons to reach through the opening between the guard and the conveyor belt to access the in-running nip point and therefore be exposed to the risk of trapping or crushing. These guards did not comply with the requirements of The Provision and Use of Work Equipment Regulations (NI) 1999.
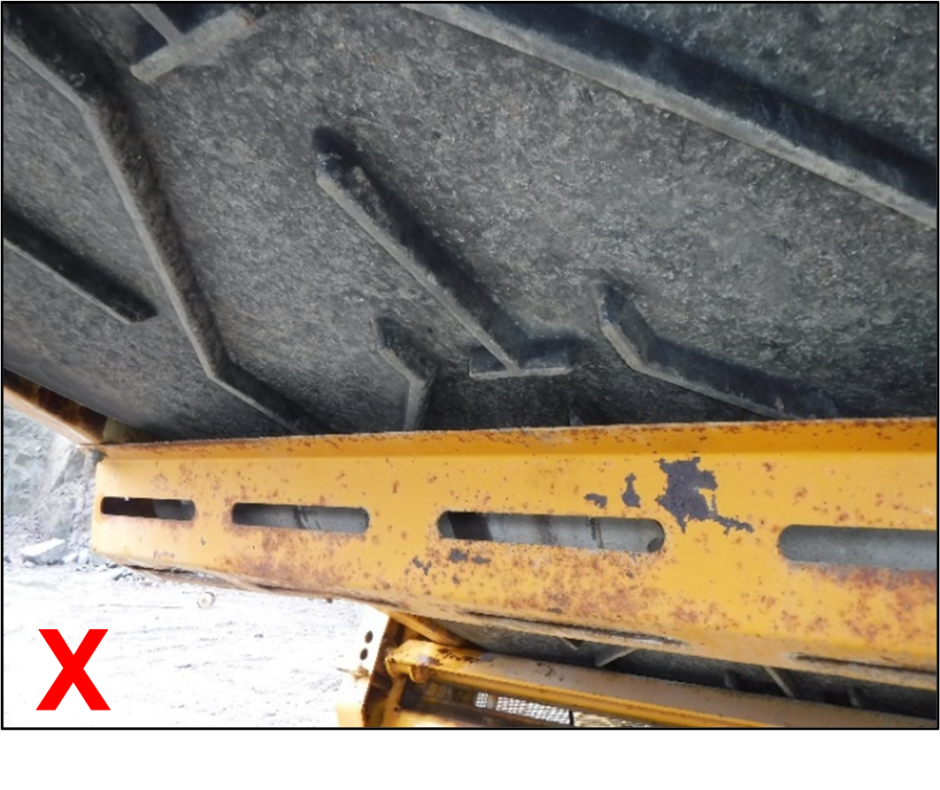
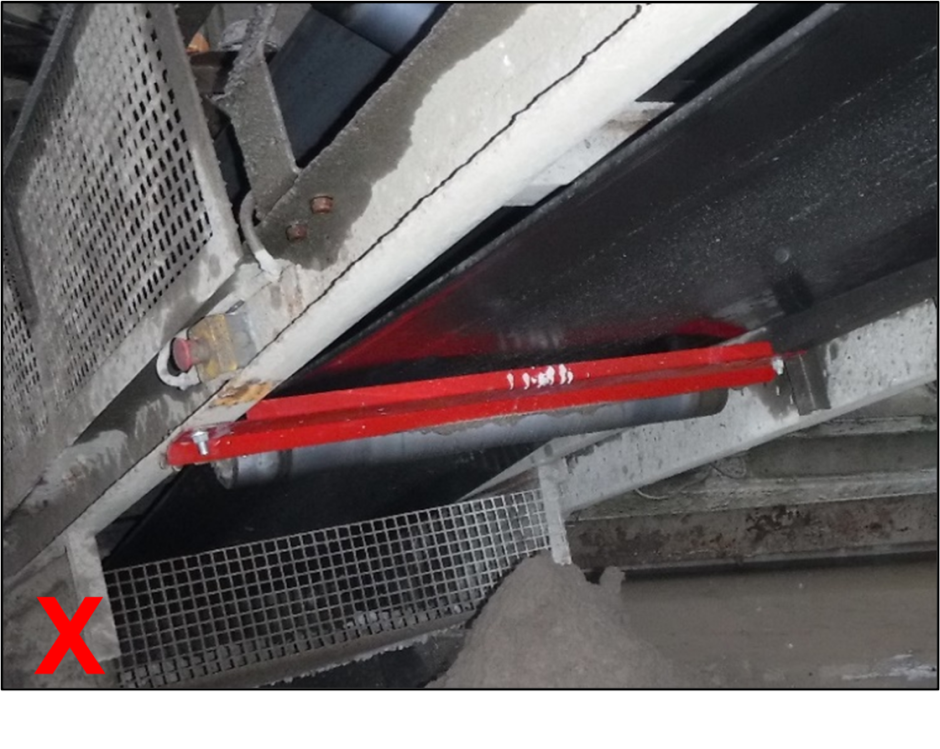
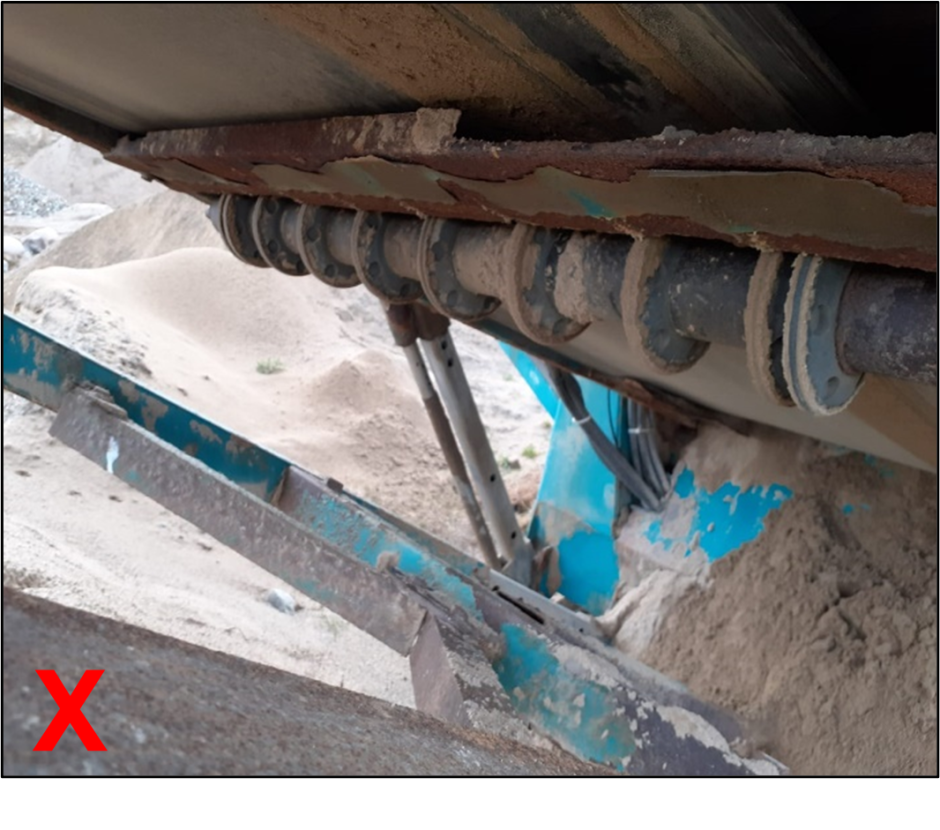
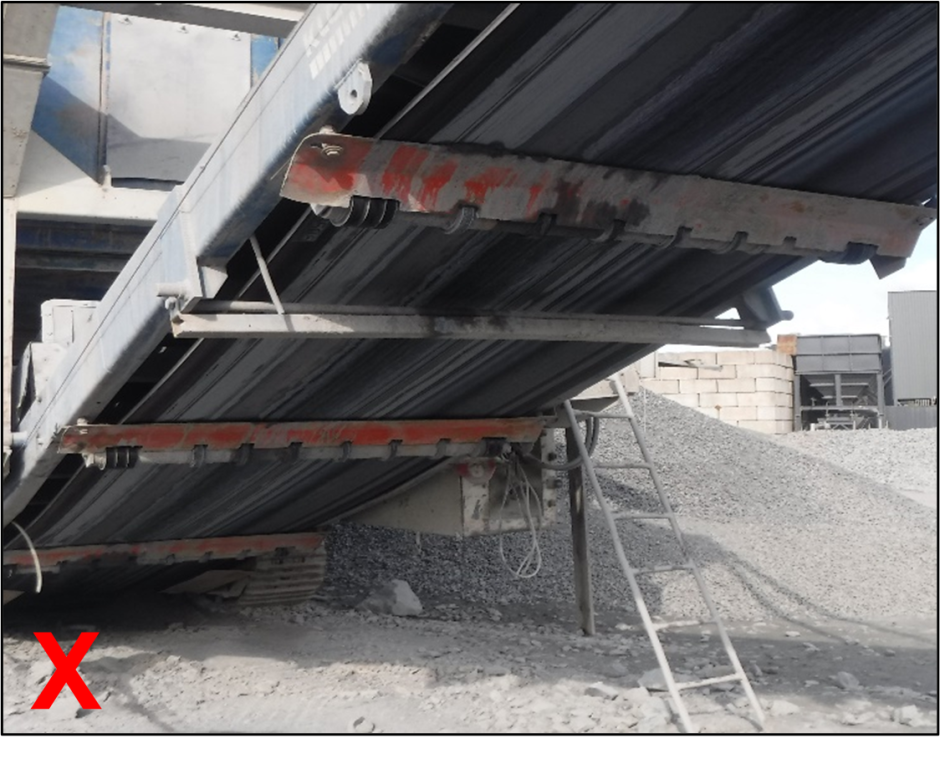